Stage 9 - Inspection
Over the years there were several different layouts for the Inspection area. In the final version, products were inspected as they were unloaded from kiln cars.
After firing, pieces were inspected for factors including glaze finish, shape, cracks and, if required, function.
Small glaze defects could be repaired with resin which was then cured with ultraviolet light. For larger repairs, a glaze paste or a partial respray would be used followed by re-firing in an intermittent kiln.
Each piece could be placed in gauges to check the shape.
Using a wooden tool the piece would be tapped. A clear ring indicated a good piece, a dull thud would indicate a cracked product. Certain designs of closet would be vacuum tested to check for leaks. Flush testing could also be carried out.
Checks would also be made by QA to ensure that products conformed to the standards.
Scrap fired pieces (pitchers) could be sent for processing and re-used in the slip process (ground pitchers).
Items that had been checked and approved were packed and transferred to the warehouse awaiting despatch.
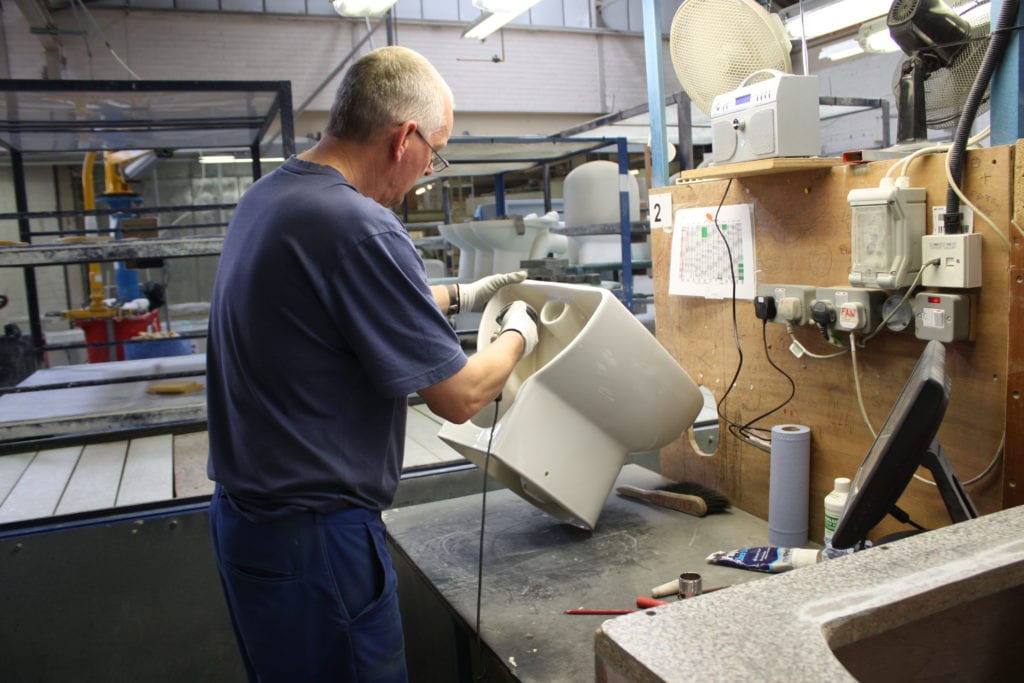